El mantenimiento predictivo es una estrategia que permite anticipar fallos en la maquinaria mediante el análisis de datos. Esta metodología se basa en las condiciones operativas reales, lo que optimiza la intervención y mejora la eficiencia. Implementar las mejores prácticas en este ámbito es esencial para reducir tiempos de inactividad y maximizar la rentabilidad. A continuación, se presentan las claves y técnicas para una gestión efectiva del mantenimiento predictivo.
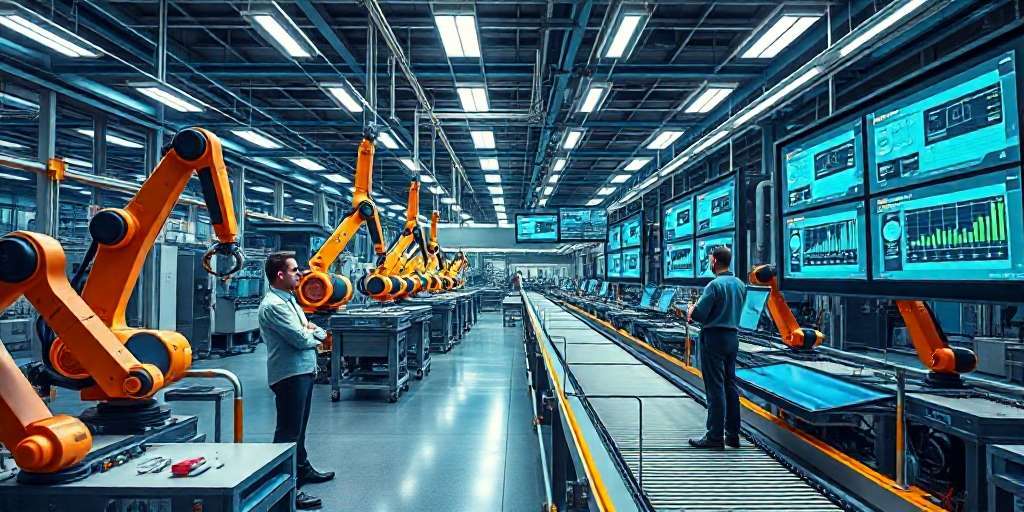
Fundamentos del Mantenimiento Predictivo
El mantenimiento predictivo se basa en técnicas avanzadas para garantizar la operatividad de la maquinaria. A través del análisis de datos, se busca minimizar los parones no planificados y optimizar los recursos, lo que reviste gran importancia en el ámbito industrial actual.
¿Qué es el mantenimiento predictivo?
El mantenimiento predictivo es una estrategia que implica el uso de tecnologías y métodos analíticos para prever y anticipar fallos en maquinaria y equipos. Esta metodología se centra en el estado actual real de los activos en lugar de seguir un calendario preestablecido de mantenimiento. Se vale del análisis de datos obtenidos de diversas fuentes, incluyendo sensores y sistemas de monitoreo, para identificar cambios o anomalías que puedan indicar un posible fallo inminente.
Importancia del mantenimiento predictivo
La implementación de un sistema de mantenimiento predictivo aporta múltiples beneficios que son cruciales para el rendimiento operativo de las empresas:
- Reducción de tiempos de inactividad: anticipar los fallos permite realizar intervenciones programadas sin impactar la producción.
- Optimización de recursos: el mantenimiento se lleva a cabo solo cuando es necesario, lo que reduce la utilización innecesaria de materiales y mano de obra.
- Prolongación de la vida útil de los equipos: al realizar mantenimientos preventivos basados en condiciones, se mejora la longevidad de los activos.
- Mejora en la seguridad laboral: al evitar fallos inesperados, se minimizan los riesgos de accidentes y lesiones en el entorno de trabajo.
Diferencias con el mantenimiento preventivo y correctivo
Para entender el mantenimiento predictivo, es esencial compararlo con otras modalidades de mantenimiento:
- Mantenimiento preventivo: se basa en realizar tareas de mantenimiento programadas a intervalos regulares, independientemente del estado real del equipo. Esto puede resultar en intervenciones innecesarias o, por el contrario, en descuidos si los intervalos no son adecuados.
- Mantenimiento correctivo: se lleva a cabo después de que ocurre un fallo, lo que resulta en tiempos de inactividad a menudo imprevistos y costosos. Este tipo de mantenimiento se considera reactivo y puede afectar gravemente la eficiencia operativa.
El mantenimiento predictivo se sitúa entre estos dos enfoques, utilizando datos y análisis para precisar el momento óptimo para realizar una intervención. Esta capacidad para anticipar permite a las empresas ser más proactivas en la gestión de sus recursos y en la planificación de sus operaciones. A través de la integración de tecnologías, el mantenimiento predictivo contribuye a la modernización y optimización de los procesos industriales.
Técnicas Principales de Mantenimiento Predictivo
El mantenimiento predictivo se basa en la recogida y análisis de datos para prever fallos en la maquinaria. A continuación se describen las técnicas más comunes utilizadas en la industria para llevar a cabo este enfoque.
Análisis de Vibraciones
El análisis de vibraciones es una de las metodologías más utilizadas en el mantenimiento predictivo. Esta técnica implica la medición y evaluación de las vibraciones generadas por la maquinaria durante su funcionamiento. Estas vibraciones, si se analizan adecuadamente, pueden proporcionar información valiosa sobre la condición de las máquinas.
Las vibraciones se registran utilizando sensores especiales que capturan los patrones de movimiento a diferentes frecuencias. Cambios en estos patrones pueden indicar problemas como desalineaciones, desequilibrios o desgaste de componentes. Los datos obtenidos se procesan mediante software de análisis, que permite identificar tendencias y anomalías que podrían llevar a fallos inminentes.
Termografía Infrarroja
La termografía infrarroja es una técnica no invasiva que utiliza cámaras térmicas para medir la temperatura de las superficies de las máquinas. Mediante esta técnica, se pueden identificar puntos calientes que podrían ser indicativos de problemas, como:
- Fricciones excesivas.
- Conexiones eléctricas defectuosas.
- Fugas de fluidos.
El análisis termográfico es particularmente útil para el mantenimiento eléctrico y mecánico, permitiendo detectar temperaturas anómalas antes de que resulten en encuentros catastróficos. La termografía se alimenta de imágenes detalladas que forman un mapa térmico, mostrándose así áreas con diferentes niveles de temperatura que facilitan la identificación de problemas.
Análisis de Aceite
El análisis de aceite se enfoca en el estado del lubricante utilizado en las máquinas. Este proceso permite detectar contaminación y desgaste, así como cambios en las propiedades del aceite que pueden afectar el rendimiento del equipo. Los aspectos clave a evaluar incluyen:
- Acidez.
- Contenido de agua.
- Viscosidad.
- Presencia de partículas contaminantes.
A través del análisis periódico del aceite, las empresas pueden prever la necesidad de reemplazos o reparaciones en los componentes mecánicos, lo que a la larga disminuye el riesgo de fallos y mejora la eficiencia operativa.
Inspección por Ultrasonido
La inspección mediante ultrasonido es otra técnica eficaz que utiliza ondas ultrasónicas para detectar irregularidades en las máquinas. Esta metodología permite identificar fugas en sistemas presurizados y ruidos anómalos en rodamientos. Gracias a su sensibilidad, el ultrasonido es capaz de localizar condiciones problemáticas con alta precisión, facilitando el diagnóstico sin requerir el desensamble del equipo.
Las pruebas ultrasonido se emplean ampliamente en compresores, válvulas y tuberías, ayudando a identificar problemas subyacentes que podrían no ser visibles a simple vista. Este enfoque proactivo favorece la detección temprana de fallos y contribuye a evitar costosas paradas en la producción.
Pruebas de Partículas Magnéticas
Las pruebas de partículas magnéticas son una técnica no destructiva utilizada para detectar grietas y fallos en superficies ferromagnéticas. Este método consiste en aplicar un campo magnético sobre la superficie del material, lo que permite revelar discontinuidades invisibles a simple vista. Las partículas magnéticas se utilizan para indicar la existencia de defectos, brindando así información crítica sobre la integridad de componentes esenciales en la maquinaria.
Estas pruebas son especialmente efectivas en aplicaciones donde la fiabilidad del material es crítica, como en ejes, engranajes y otros componentes que operan bajo estrés constante. Esto asegura una mayor seguridad y durabilidad de los equipos.
Implementación de un Programa de Mantenimiento Predictivo
La implementación de un programa de mantenimiento predictivo requiere un enfoque metódico y bien planificado. Cada aspecto de este proceso es esencial para asegurar que la estrategia de mantenimiento sea eficiente y sostenible a largo plazo.
Formación y Capacitación del Personal
El éxito de un programa de mantenimiento predictivo está íntimamente relacionado con la formación del personal involucrado. La capacitación adecuada garantiza que los trabajadores comprendan las técnicas y herramientas necesarias para llevar a cabo el mantenimiento de manera efectiva.
- Desarrollar programas de formación específicos en técnicas de mantenimiento predictivo.
- Incluir formación en el uso de tecnologías avanzadas y herramientas de análisis.
- Promover un ambiente de aprendizaje continuo para seguir actualizado con las mejores prácticas del sector.
Establecimiento de Objetivos y Metas Claras
Antes de iniciar el programa, es crucial definir los objetivos que se buscan alcanzar. Estos objetivos deben ser específicos, medibles, alcanzables, relevantes y temporales (SMART).
- Reducir los tiempos de inactividad de la maquinaria.
- Aumentar la eficiencia operativa de los equipos.
- Disminuir los costos asociados al mantenimiento de máquinas.
- Mejorar la seguridad laboral a través de la anticipación de fallos.
Definición de Activos Críticos
No todos los activos dentro de una empresa requieren las mismas estrategias de mantenimiento. Identificar cuáles son los equipos y maquinarias críticas para el funcionamiento operativo es fundamental.
- Clasificar los activos en función de su impacto en la producción.
- Comenzar con equipos menos críticos para validar el enfoque del programa.
- Expandir la implementación a máquinas de mayor importancia tras obtener experiencia con los activos iniciales.
Recopilación y Análisis de Datos
Una de las bases del mantenimiento predictivo es la recopilación y análisis de datos. La información precisa y en tiempo real permite tomar decisiones informadas sobre cuándo y cómo realizar intervenciones.
Uso de Tecnología IoT
La Internet de las Cosas (IoT) se ha convertido en un aliado clave en la recopilación de datos. Sensores conectados a la maquinaria permiten monitorizar el desempeño y el estado de los equipos en tiempo real.
Sistemas de Monitorización en Tiempo Real
Estos sistemas facilitan la supervisión continua de los activos. A través de plataformas avanzadas, se pueden visualizar los parámetros operativos y recibir alertas ante cualquier anomalía.
Implementación de Tecnología y Herramientas Apropiadas
La selección de la tecnología y las herramientas adecuadas es fundamental para el éxito del mantenimiento predictivo. Invertir en sistemas de última generación garantiza una recopilación y análisis de datos efectivos.
- Utilizar software de análisis predictivo que facilite la interpretación de datos recopilados.
- Integrar sensores y dispositivos que ofrezcan información precisa sobre el estado de los activos.
- Implementar sistemas que comuniquen datos de forma eficiente entre diferentes equipos y niveles organizativos.
Monitoreo y Ajuste Continuo
Una vez en funcionamiento, el programa de mantenimiento predictivo debe ser objeto de monitoreo constante. Evaluar los resultados y realizar ajustes es esencial para garantizar su efectividad.
- Revisar periódicamente los indicadores de rendimiento establecidos.
- Ajustar las estrategias en función de los resultados obtenidos y la evolución de las condiciones operativas.
- Fomentar la retroalimentación del personal involucrado en el proceso para mejorar continuamente las prácticas implementadas.
Herramientas y Tecnologías para el Mantenimiento Predictivo
Las herramientas y tecnologías son fundamentales para la implementación eficaz del mantenimiento predictivo. Estas soluciones permiten la monitorización continua y el análisis detallado de las condiciones de operación de la maquinaria, favoreciendo la detección temprana de posibles fallos.
Sensores y Dispositivos de Medición
Los sensores y dispositivos de medición son componentes clave en un sistema de mantenimiento predictivo. Su función principal es recoger datos en tiempo real sobre el estado de la maquinaria. Existen diferentes tipos de sensores, cada uno diseñado para capturar parámetros específicos, lo que contribuye a una visión integral del rendimiento del equipo.
- Sensores de Vibración: Miden las vibraciones producidas por los componentes mecánicos. Un cambio irregular en los patrones de vibración puede señalar problemas de desalineación o desgaste.
- Sensores de Temperatura: Monitorizan la temperatura de las piezas y sistemas críticos. Un incremento en la temperatura puede indicar una fricción anormal o fallos en los componentes eléctricos.
- Sensores de Presión: Son esenciales para sistemas hidráulicos y neumáticos. La variación en la presión puede ser un indicativo de fugas o fallos en las válvulas.
- Sensores de Humedad: Ayudan a detectar la presencia de humedad en entornos sensibles. Esto es crucial para prevenir la corrosión y el deterioro prematuro de las máquinas.
Software de Análisis Predictivo
Los sistemas de software de análisis predictivo procesan los datos recogidos por los sensores para identificar tendencias y patrones que pueden anticipar fallos. Estas herramientas son responsables de transformar la información bruta en conocimiento útil para la toma de decisiones.
- Análisis de Datos: Facilita la comprensión de grandes volúmenes de datos y su interpretación en contexto. Esto permite a los técnicos identificar problemas potenciales y priorizar las intervenciones.
- Modelos Predictivos: Utilizan algoritmos avanzados para prever el comportamiento futuro de la maquinaria. Estos modelos se alimentan de datos históricos y actuales para generar pronósticos precisos.
- Visualización de Datos: Herramientas que permiten representar gráficamente los datos analizados, facilitando su comprensión. Los paneles de control proporcionan una vista rápida sobre la salud de las máquinas.
Integración de Sistemas
La integración de sistemas es un aspecto crucial del mantenimiento predictivo moderno. Consiste en interconectar diferentes tecnologías y plataformas para crear un ecosistema cohesionado que optimiza la recopilación y análisis de datos.
- Sistemas IoT (Internet de las Cosas): El uso de dispositivos IoT permite la conexión de máquinas a la red, facilitando la transmisión continua de datos. Esto permite una monitorización en tiempo real y mejora la capacidad de respuesta ante problemas emergentes.
- Plataformas de Gestión de Mantenimiento: Software que centraliza la información sobre el estado de los activos. Estas plataformas ayudan en la planificación de tareas y el seguimiento de intervenciones, optimizando recursos y tiempo.
- Interoperabilidad: Es fundamental que los diferentes sistemas puedan comunicarse entre sí sin problemas. La interoperabilidad garantiza que todos los componentes del sistema funcionen de manera integrada y eficaz.
Beneficios del Mantenimiento Predictivo
El mantenimiento predictivo ofrece numerosas ventajas que impactan positivamente en la operativa de las empresas. Su correcta implementación no solo evita fallos, sino que también mejora el rendimiento general de la maquinaria y optimiza el uso de recursos a largo plazo.
Reducción de Tiempos de Inactividad
Una de las principales aportaciones del mantenimiento predictivo es la capacidad de reducir los tiempos de inactividad. Detectar problemas potenciales antes de que se conviertan en fallos críticos permite realizar intervenciones programadas que no interrumpen la producción. Esto se traduce en una continuidad operativa más fluida y menos sorpresas, lo cual es esencial en entornos industriales competitivos.
Gracias a la anticipación que ofrece esta metodología, las empresas pueden planificar las paradas necesarias para el mantenimiento, evitando así paradas imprevistas. Esta planificación se traduce en una mejor gestión del tiempo de producción.
Optimización de Recursos
El mantenimiento predictivo también contribuye a la optimización de recursos, tanto humanos como materiales. Al prever y actuar sobre problemas emergentes, se reduce la necesidad de intervenciones urgentes, lo que permite una mejor asignación del personal técnico. Este enfoque no solo utiliza de manera más eficiente a los trabajadores, sino que también minimiza el gasto en piezas de recambio y en otros consumibles.
La eficiencia en el uso de recursos ayuda a las empresas a gestionar sus presupuestos de manera más efectiva, ya que los gastos inesperados suelen ser mayores que aquellos que se pueden anticipar y planificar. De este modo, las organizaciones alcanzan un mejor control sobre sus costos operativos.
Prolongación de la Vida Útil de la Maquinaria
El mantenimiento predictivo se traduce en una notable prolongación de la vida útil de la maquinaria. Al mantener los equipos en condiciones óptimas y realizar intervenciones solo cuando se requieren, se evita el desgaste excesivo y se asegura un funcionamiento más sostenible. Esta práctica reduce la necesidad de reemplazo frecuente de equipos, lo que representa un ahorro significativo a largo plazo.
Además, cuidar adecuadamente de los activos industriales incrementa su fiabilidad, lo cual es esencial para mantener la calidad de la producción. Cuando las máquinas funcionan de manera eficiente a lo largo del tiempo, la empresa puede mantener altos estándares de producción sin la amenaza de fallos inesperados que comprometan la calidad del producto final.
Casos de Uso y Ejemplos Reales
El mantenimiento predictivo ha demostrado ser una estrategia efectiva en diversas industrias. A continuación se presentan ejemplos concretos que ilustran su aplicación y los resultados obtenidos en diferentes contextos.
Ejemplos de Mantenimiento Predictivo en la Industria
El mantenimiento predictivo se ha implementado en múltiples sectores industriales, mostrando su capacidad para mejorar la eficiencia operativa y reducir costos. Algunos ejemplos destacados son:
- Industria Automotriz: En fábricas de automóviles, el uso de análisis de vibraciones y termografía infrarroja ayuda a predecir fallos en maquinaria crítica. Esto permite programar paradas para mantenimiento de manera eficiente, evitando retrasos en la producción.
- Plantas de Generación Eléctrica: El análisis de aceite y la inspección por ultrasonido se utilizan para detectar problemas en generadores y turbinas. Gracias a ello, se minimizan las interrupciones en el suministro eléctrico y se optimiza la disponibilidad de las instalaciones.
- Sector Petroquímico: Las pruebas de partículas magnéticas son esenciales para el mantenimiento de estructuras críticas. Este método permite identificar fallos en equipos que operan en condiciones extremas, garantizando la seguridad y la continuidad operativa.
- Manufactura de Alimentos: Las fábricas de alimentos utilizan sensores IoT para monitorizar el estado de las maquinarias de procesamiento. Esto permite una detección temprana de problemas y una mejora en la seguridad alimentaria mediante el mantenimiento adecuado de los equipos.
Resultados Obtenidos en Diferentes Sectores
Los casos prácticos de mantenimiento predictivo han reflejado mejoras significativas en varios aspectos clave. Los resultados más destacados incluyen:
- Reducción de Tiempos de Inactividad: La anticipación a posibles fallos ha permitido disminuir los tiempos de inactividad en un 30% en algunas industrias, como la automotriz, manteniendo así la producción en niveles óptimos.
- Optimización de Recursos: Se ha observado una disminución del 20% en los costos de mantenimiento en sectores como el energético, gracias a una mejor planificación de intervenciones basadas en datos reales y análisis de tendencias.
- Prolongación de la Vida Útil de la Maquinaria: En plantas petroquímicas, el correcto seguimiento de las condiciones operativas ha aumentado la vida útil de los equipos en hasta un 25%, evitando reemplazos costosos y aumentando el ROI.
- Mejora en la Seguridad: La implementación de mantenimiento predictivo ha contribuido a la reducción de incidentes laborales en un 40% en el sector de manufactura, lo que refleja un ambiente de trabajo más seguro y confiable.
Desafíos y Soluciones en el Mantenimiento Predictivo
La implementación de un programa de mantenimiento predictivo puede enfrentar varios retos. Estos desafíos pueden surgir de diversos factores, como la resistencia al cambio, la falta de conocimientos y la adaptación a tecnologías emergentes. A continuación, se exploran algunos de estos problemas y las soluciones correspondientes.
Problemas Comunes y Cómo Resolverlos
Entre los problemas más frecuentes se pueden mencionar:
- Resistencia al cambio: Muchos empleados pueden estar acostumbrados a métodos tradicionales de mantenimiento y mostrar reticencia a adoptar nuevas tecnologías. Para superar esto, es fundamental realizar talleres y sesiones de formación que expliquen los beneficios del mantenimiento predictivo y su impacto positivo en la eficiencia operativa.
- Falta de formación técnica: El personal puede carecer de las habilidades necesarias para utilizar herramientas y técnicas de mantenimiento predictivo. Esto se puede solucionar mediante programas de capacitación que incluyan formación práctica y el uso de simuladores. Es importante invertir en la actualización constante del personal.
- Integración de datos: La recopilación y análisis de datos puede verse obstaculizada por la falta de un sistema unificado. Para resolver este inconveniente, es recomendable adoptar plataformas integradoras que centralicen la información de diferentes fuentes, facilitando la monitoreo en tiempo real y el análisis de datos.
- Costes iniciales: La inversión en tecnología y formación puede ser elevada al principio. Para gestionar este reto, las empresas deben planificar un presupuesto a largo plazo que contemple la gradual implementación de tecnologías, resaltando que el retorno de inversión se verá reflejado en la reducción de costes operativos a medida que se implementen las mejoras.
Adaptación a Nuevas Tecnologías
La rápida evolución tecnológica puede representar otro desafío. Las empresas deben adaptarse a nuevas herramientas y sistemas para mantenerse competitivas en un mercado en constante cambio. Esto puede incluir la integración de tecnologías como el Internet de las Cosas (IoT) y sistemas inteligentes de análisis predictivo.
La adaptación a estas tecnologías no solo requiere inversión, sino también tiempo y un enfoque estratégico. Algunas soluciones incluyen:
- Evaluación de tendencias: Las empresas deben estar al tanto de las últimas tendencias en mantenimiento predictivo para identificar oportunidades que puedan aplicar en su funcionamiento diario.
- Colaboración con proveedores: Trabajar estrechamente con proveedores tecnológicos puede facilitar la transición, ya que estos pueden ofrecer soporte, consejos y formación específica acerca de las nuevas herramientas implementadas.
- Pruebas piloto: Realizar pruebas a pequeña escala con nuevas tecnologías antes de su implementación completa puede ayudar a detectar problemas y ajustes necesarios sin un gran riesgo financiero.
Futuro del Mantenimiento Predictivo
El mantenimiento predictivo está en constante evolución, impulsado por las innovaciones tecnológicas y las tendencias emergentes que transforman la manera en que se gestionan las maquinarias. Se espera que en los próximos años, estas tendencias redefinan los estándares de la industria.
Tendencias Emergentes
El futuro del mantenimiento predictivo estará marcado por diversas tendencias que impactarán en la forma en que las organizaciones implementan sus estrategias de mantenimiento. Algunas de las más significativas incluyen:
- Inteligencia Artificial y Aprendizaje Automático: La integración de la inteligencia artificial permitirá mejorar la precisión del análisis de datos y la detección de anomalías. Los sistemas aprenderán de patrones previos, optimizando intervenciones y reduciendo errores humanos.
- Mantenimiento Autónomo: La automatización de tareas de mantenimiento se convierte en una realidad. Equipos que pueden diagnosticar y realizar reparaciones de forma independiente cambiarán el enfoque hacia una gestión más eficiente.
- Integración de IoT: La conectividad IoT permitirá la recopilación de datos en tiempo real desde múltiples dispositivos y sensores. Esto facilitará un análisis más profundo y una respuesta más rápida a las condiciones operativas.
- Analítica Predictiva Avanzada: Se espera que la analítica de datos evolucione hacia modelos más complejos, utilizando grandes volúmenes de datos para prever fallos con mayor antelación.
Innovaciones Tecnológicas
Las innovaciones tecnológicas no solo optimizan el mantenimiento predictivo, sino que también crean nuevas oportunidades. Entre las más relevantes se incluyen:
- Sensores Avanzados: Con avances en la tecnología de sensores, ahora es posible monitorizar variables que antes eran difíciles de captar. Sensores más precisos para vibraciones, temperatura y humedad mejorarán la detección de problemas en fases tempranas.
- Software de Gestión de Mantenimiento: Las herramientas que facilitan la gestión de datos y la planificación de mantenimiento se vuelven más accesibles y potentes. Esto permite que las empresas personalicen sus enfoques según sus necesidades específicas.
- Realidad Aumentada y Virtual: Estas tecnologías están comenzando a ser utilizadas para la formación del personal y la asistencia remota, mejorando la capacidad de respuesta ante fallos y ayudando en el diagnóstico sin la necesidad de desplazamiento físico.
- Blockchain: Aunque todavía en sus primeras etapas de adopción, esta tecnología puede aportar transparencia y seguridad en el seguimiento de mantenimiento, garantizando la integridad de los datos y facilitando la colaboración entre diferentes partes interesadas.
Mejores Prácticas para Gestionar el Mantenimiento Predictivo
El mantenimiento predictivo se beneficia enormemente de la implementación de prácticas sistemáticas y bien definidas que garantizan la eficiencia y efectividad del proceso. En esta sección, se presentan las prácticas que deben considerarse para gestionar adecuadamente esta metodología.
Definición y Seguimiento de Indicadores de Rendimiento
Establecer indicadores de rendimiento clave (KPI) es esencial para evaluar la eficacia de un programa de mantenimiento predictivo. Estos indicadores deben ser medibles y estar alineados con los objetivos estratégicos de la organización. Entre los KPI comunes se pueden incluir:
- Tasa de fallos no planificados
- Tiempo medio entre fallos (MTBF)
- Costos de mantenimiento por unidad de producción
- Porcentaje de intervenciones predictivas en comparación con las preventivas
El seguimiento constante de estos indicadores permite identificar áreas de mejora y ajustar las estrategias de mantenimiento en función de los resultados obtenidos. Esto no solo aumenta la eficiencia operativa, sino que también optimiza el uso de recursos.
Mantenimiento de un Histórico de Datos
La recopilación y el manejo de datos históricos son pilares fundamentales del mantenimiento predictivo. Almacenar información sobre el rendimiento de la maquinaria, así como sobre las intervenciones realizadas, ayuda a generar un background que puede ser útil para el análisis futuro. Los aspectos más importantes a considerar son:
- Registro detallado de las intervenciones efectuadas, incluyendo la fecha, tipo de mantenimiento y resultados obtenidos.
- Almacenamiento de datos de sensores y equipos de monitoreo, que permite el análisis de tendencias a lo largo del tiempo.
- Análisis de los datos recopilados para la identificación de patrones que podrían predecir fallos en el futuro.
Un historial de datos bien gestionado resulta vital para tomar decisiones informadas y proactivas que impulsen el rendimiento del equipo y el proceso productivo en general.
Colaboración y Comunicación Efectiva en el Equipo
La comunicación fluida y la colaboración entre los diferentes departamentos y equipos de trabajo son factores esenciales para el éxito del mantenimiento predictivo. Esto incluye:
- Realización de reuniones periódicas para compartir información sobre el estado del equipo y las intervenciones realizadas.
- Fomentar un ambiente de trabajo en el que todos los integrantes del equipo se sientan libres de expresar sus observaciones o inquietudes sobre el funcionamiento de la maquinaria.
- Uso de herramientas digitales que faciliten la comunicación y el acceso a datos relevantes en tiempo real.
Una correcta coordinación entre los diferentes sectores garantiza que todos estén alineados con los objetivos del mantenimiento predictivo, lo que favorece un enfoque integral y proactivo en la gestión de la maquinaria.